On a Wing and a Prayer at Boeing

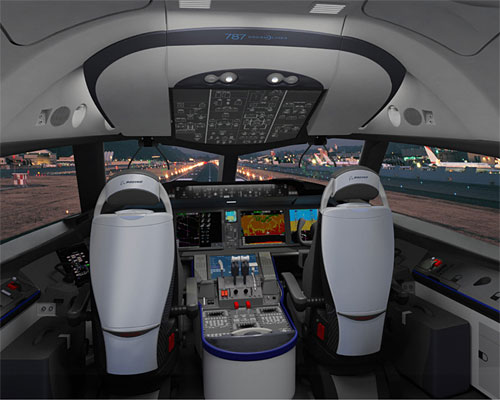
BusinessWeek Online 06/07/2006
Author: Stanley Holmes
For Boeing (BA ) the 787 Dreamliner, with its radical new lightweight design, represents far more than a potentially juicy profit stream. The carbon-fiber-reinforced plastic aircraft is supposed to be the symbol of a new Boeing -- a visionary company that has transcended its recent ethical scandals, designed the most innovative commercial plane ever, and devised the most sophisticated manufacturing process in history to produce the aircraft. But as crucial deadlines loom, BusinessWeek has learned that Boeing's engineers are wrestling with several significant technical and production problems that could threaten the scheduled 2008 delivery of the jetliner.
At a time when Boeing has left itself with little margin for error, the wide-ranging series of glitches could create a domino effect if not resolved quickly. The most important piece of bad news -- the fuselage section, the big multi-part cylindrical barrel that encompasses the passenger seating area, has failed in company testing. That's forcing Boeing to make more sections than planned, and to reexamine quality and safety concerns.
Elsewhere in the aircraft, suppliers are struggling to meet Boeing's exacting technological standards and ambitious production deadlines. The first two nose sections, for instance, were deemed unacceptable by Boeing. Software programs designed by a variety of manufacturers are having trouble talking to one another. And the overall weight of the airplane is still too high-- especially the single biggest part of the 787, the carbon-fiber wing.
BIG PAYOFF. A light, strong plane is the big payoff for the huge technical risk Boeing is taking in crafting parts out of composites. Small wonder that as the entire Boeing team prepares to build the first airplane, tensions among engineers have erupted into shouting matches, say people familiar with the matter.
Technical glitches, missed deadlines, and stretched nerves are par for the course with new planes. But far more than a new plane is at stake. Boeing has undertaken a grand business experiment with the Dreamliner. In a bid to tap the best talent and hold down costs, the aerospace icon has engaged in extreme outsourcing, leaving it highly dependent on a far-flung supply chain that includes 43 "top-tier" suppliers in 12 countries. It is the first time Boeing has ever outsourced the most critical areas of the plane, the wing and the fuselage. About 80% of the Dreamliner is being fabricated by outside suppliers, vs. 51% for existing Boeing planes.
The Dreamliner's mounting challenges call into question whether such a radical business model can succeed, and whether the advantages of collaboration on such a scale are outweighed by the loss of logistical control. For Boeing in particular, it raises the question of whether the company is entering a danger zone that could result in a serious blow to its credibility. In the years since Boeing's epic production disaster in the late 1990s, the company has regained much of its reputation and the ground it had lost to European rival Airbus. The Dreamliner has been central to that remarkable revival, racking up a record 350 firm orders in two years. That has forced Airbus to go on the defensive and rethink its midsize plane strategy.
FINANCIAL RISKS. There could also be large financial penalties for Boeing if problems result in big delays. With demand hot, the manufacturer is mulling whether to raise production rates after 2010 from 7 to 10 airplanes a month, and possibly higher. Glitches in the new fuselage-making process could put that decision on hold, squeezing the potential peak revenue and operating profit. Boeing typically receives the major portion of its revenue when it delivers a finished airplane.
In an interview with BusinessWeek, Boeing 787 Vice-President Michael Bair acknowledged the various problems. But he insists that the Dreamliner will enter service in 2008 as planned. "Yes, the last barrel failed," Bair says. "We knew it could happen. Did we wish it would happen? No." Bair adds that "everybody is struggling a bit and struggling to various degrees." He remains optimistic, if guardedly so, about meeting the 2008 deadline. "Right now, everything looks O.K. in terms of meeting our entry into service dates for the 787," Bair told reporters in a May 22 conference call. "But as you all know, new airplanes are really hard to do."
The last time Boeing staked its reputation on its production prowess, during the 1997-98 boom cycle, its factories tried to build too many planes too quickly and wound up having to make a disastrous shutdown of the assembly lines. The fallout cost Boeing $2.5 billion in delivery penalties and cost overruns, and nearly destroyed its reputation as the world's leading developer of commercial jets. Many believe the fierce internal rivalries between Boeing units at the time created a focus on getting results at any cost, and led to the very public unraveling of the company in a long series of ethics scandals.
WALLPAPER PROJECT. The first big sign of struggle with the 787 surfaced three weeks ago at Boeing's Developmental Center in south Seattle. That's when engineers discovered that worrisome bubbles were developing in the skin of the fuselage during the process of baking the plastic composite tape in big oven-like machines.
Think of the operation as a massive wallpapering exercise. The "paper" is wide tape that's loosely woven from superstrong carbon fibers, then soaked in a honey-thick mixture of polymers. The gooey tapes are plastered on the inside of molds, and then cooked. The heat triggers a chemical reaction that turns the polymers into a hard, super-sturdy structure. The advantages of a carbon-fiber fuselage are enormous in saving weight, reducing costly inspection checks, and simplifying assembly of the plane.
But the main challenge is the sheer size of the fuselage sections. These require multiple layers of carbon-fiber tape to assure structural integrity. However, each added layer increases the likelihood of variations or flaws, say composite experts, such as bubbles on the skin. Bubbles could weaken the material and eventually cause cracks by allowing water to seep under the surface, then freeze up and expand at high altitudes, raising the possibility that the fuselage could crack under extreme conditions. Bair says Boeing has located the source of the problem.
Other trouble spots have been the efforts at electronic integration. The Dreamliner will rely on electric power, rather than a more mechanical process, to signal the controls from the flight deck to the rest of the plane, thus reducing weight and complexity. But Boeing issued key protocols late to suppliers. That, combined with the fact that the software systems are not integrating smoothly, has delayed the integration effort.
What's more, suppliers such as Smiths, Honeywell (HON ), and Rockwell (COL) are fierce competitors that have been corralled into being teammates on the 787 program. As each vendor struggled to get its software to talk to the others, competitive juices boiled, and partners turned into the hardened competitors they usually are. "I'm used to knowing who my enemy is every step of the way," says one supplier familiar with the matter. "But now I'm working with the enemy."
Bair acknowledges the communications problems -- and admits that nobody inside of Boeing thought building the 787 would be easy. After all, the company decided to bet on pushing the boundaries of the possible. "If everything was going perfect," he says, "it [would mean] you weren't trying hard enough.
0 Comments:
Post a Comment
<< Home